course
Industrial Internet of Things(Industry 4.0)

Sunset
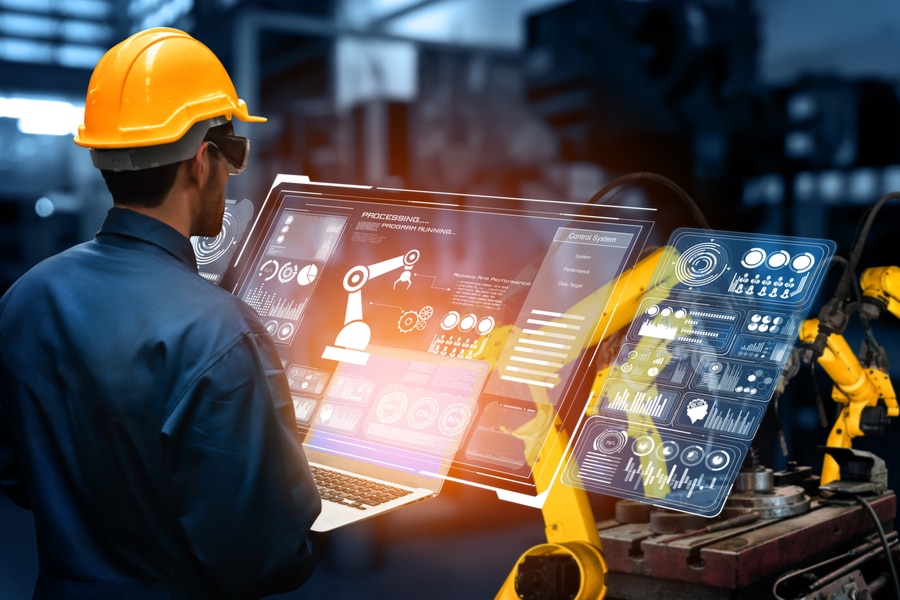
Beautiful
night

Sunshine
Vision Robotic India Pvt Ltd is one of the major training company in India that provides the best Industrial training and placement in the Advanced level Automation field. If you are planning to become an Advanced Automation Engineer then your better option would be to join our Advanced-level Industrial Automation Engineer course in Vision Robotic India Pvt Ltd.. If you complete the Advanced Industrial Automation Engineer course from Vision Robotic, you will get national & international certification. One of the major advantages of choosing a career in Automation is that it’s a good-paying job, better growth & sustainability in your career
Vision Robotic will provide a career path for freshers with a career path in the industrial automation Sector. This course will provide you with the required skills to perform in an industrial plant. During this course, you will get on-demand skills that will be useful for your future in industrial automation. You will be trained by industrial professionals and the syllabus of this course is designed by industrial professionals. You will be part of several industrial projects and this will improve your job-ready skills.
India is ready to turn into a worldwide assembling centre by offering boundaries like savvy assembling, quality, and severe conveyance plans. The least necessities to support in the worldwide market are a-list quality, severe adherence to conveyance plans, and minimal expense. To accomplish these three targets, there is no other option except to involve computerized machines for assembling.
As the Automation area increases steadily, every industry utilizes mechanized machines. There is no option for a robotized machine. Expanding demand for robotized machines results in expanding interest for machine producers. A client of a mechanized machine needs an upkeep designer to investigate the machines. A maker of robotized machines needs configuration engineers, developers, and administration engineers. Along these lines, in a perfect world, each assembling industry would like to utilize computerization engineers who investigate or configure control arrangements of machines without any help.
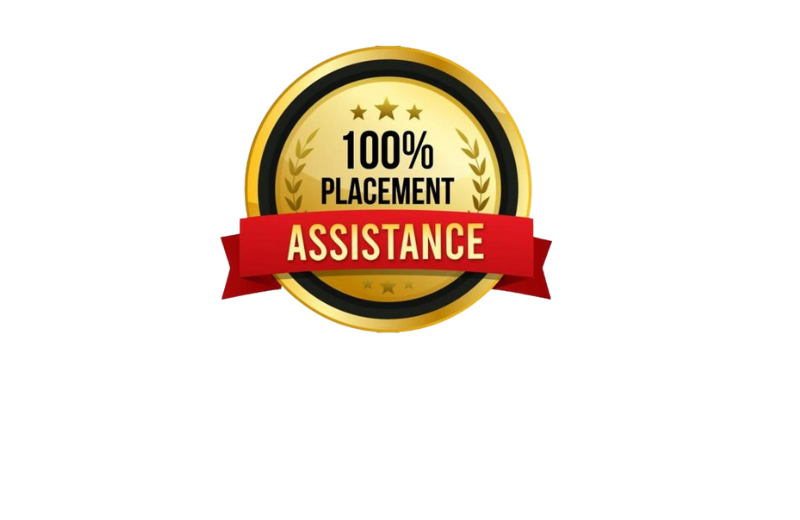
Course Contents
• Difference between Industry 3.0 and 4.0 •
• Core elements and technologies of Industry 4.0, e.g. - RFID, Big data, NFC, etc.
• M2M communication, vertical and horizontal integration, decentralized, etc. •
• Social-technological developments and their consequences.
• I 4.0 Business Models and creating new business ideas. •
• Bottom-up and Top-Down strategies to implement Industry 4.0 •
• Competences development Industry 4.0 •
• Change Management Industry 4.0 •
• Hands-on exercises with Industry 4.0 Trainer Kit
On-Site Practical Exposure
• Industry-1
• Industry-2
• Industry-3
Projects
• Level-1
• Level-2
• Level-3
** The above is the Lite syllabus and doesn’t cover the full syllabus. To get the full syllabus Book a Free Demo Now
Training on the followings Brands
Who Should Attend
- Programmers
- Erection & commissioning engineers
- Project Engineers
- Service Engineers
- Maintenance Engineers
- Machine Operators
- Software Engineers
- IoT developers
- Operation Engineers
- Application Engineers
Benefits of Training from us
- Designed for Working Professionals
- Personalized mentorship sessions
- Dedicated career support
- Doubt-Solving with Expert Industry mentors
- Proactive Program Support
- Job Assistance with Top Firms
- Syllabus is designed by Industry Experts
- Virtual Lab Facility
- 100% Placement Assistance
- National & International Certifications
Our Channel Partners
Frequently Asked Questions
What is PLC ?
- A programmable logic controller (PLC) or programmable controller is an industrial computer that has been ruggedized and adapted for the control of manufacturing processes, such as assembly lines, machines, robotic devices, or any activity that requires high reliability, ease of programming, and process fault diagnosis.
- PLCs can range from small modular devices with tens of inputs and outputs (I/O), in a housing integral with the processor, to large rack-mounted modular devices with thousands of I/O, which are often networked to other PLC and SCADA systems. They can be designed for many arrangements of digital and analog I/O, extended temperature ranges, immunity to electrical noise, and resistance to vibration and impact.
- PLCs were first developed in the automobile manufacturing industry to provide flexible, rugged, and easily programmable controllers to replace hard-wired relay logic systems. Dick Morley, who invented the first PLC, the Modicon 084, for General Motors in 1968, is considered the father of PLC.
- A PLC is an example of a hard real-time system since output results must be produced in response to input conditions within a limited time, otherwise unintended operation may result. Programs to control machine operation are typically stored in battery-backed-up or non-volatile memory.
What is HMI ?
- Human Machine Interface, often known by the acronym HMI, refers to a dashboard or screen used to control machinery. Line operators, managers, and supervisors in the industry rely on HMIs to translate complex data into useful information.
- For example, they use HMIs to monitor machinery to make sure it’s working properly. Easy-to-understand visual displays give meaning and context to near real-time information about tank levels, pressure and vibration measurements, motor and valve status, and other variables.
- But the advanced capabilities of today’s HMIs enable managers and supervisors to do much more than control processes. Using historical and trending data they offer vast new opportunities to improve product quality and make systems more efficient.
- For all these reasons, HMIs play a key role in the smooth and effective running of factories and manufacturing operations. However, not all HMIs are created the same.
What is SCADA ?
- SCADA (supervisory control and data acquisition) is a category of software applications for controlling industrial processes, which is the gathering of data in Real Time from remote locations in order to control equipment and conditions. SCADA provides organizations with the tools needed to make and deploy data-driven decisions regarding their industrial processes.
- One of the most commonly used types of industrial control systems, SCADA can be used to manage almost any type of industrial process.
- SCADA systems include hardware and software components. The hardware gathers and feeds data into field controller systems, which forward the data to other systems that process and present it to a human-machine interface (HMI) promptly. SCADA systems also record and log all events for reporting process status and issues. SCADA applications warn when conditions become hazardous by sounding alarms.
What is VFD ?
A variable frequency drive (VFD) is a type of motor controller that drives an electric motor by varying the frequency and voltage of its power supply. The VFD also can control the ramp-up and ramp-down of the motor during start or stop, respectively. Even though the drive controls the frequency and voltage of power supplied to the motor, we often refer to this as speed control, since the result is an adjustment of motor speed. There are many reasons why we may want to adjust this motor speed.
- To Save energy and improve system efficiency
- •Convert power in hybridization applications
- Match the speed of the drive to the process requirements
- Match the torque or power of a drive to the process requirements
- Improve the working environment
- Lower noise levels, for example from fans and pumps
- Reduce mechanical stress on machines to extend their lifetime
- Shave peak consumption to avoid peak-demand prices and reduce the motor size required
What is Servo Drive ?
- Set tasks, receive work servo drive receives a command signal from a control system, amplifies the signal, and transmits electric current to a servo motor in order to produce motion proportional to the command signal. Typically, the command signal represents a desired velocity, but can also represent a desired torque or position. A sensor attached to the servo motor reports the motor's actual status back to the servo drive. The servo drive then compares the actual motor status with the commanded motor status. It then alters the voltage, frequency or pulse width to the motor so as to correct for any deviation from the commanded status.
- In a properly configured control system, the servo motor rotates at a velocity that very closely approximates the velocity signal being received by the servo drive from the control system. Several parameters, such as stiffness (also known as proportional gain), damping (also known as derivative gain), and feedback gain, can be adjusted to achieve this desired performance. The process of adjusting these parameters is called performance tuning.
- Although many servo motors require a drive specific to that particular motor brand or model, many drives are now available that are compatible with a wide variety of motors, and manage projects.
What is Encoder ?
- In general an encoder is a device or process that converts data from one format to another. In position sensing, an encoder is a device that can detect and convert mechanical motion to an analog or digital coded output signal. More specifically, it measures the position, while velocity, acceleration, and direction can be derived from the position in either linear or rotary movement.
- Different functionality of encoders comes from different physical principles of operation, outputs, communication protocols, etc.
What is PID Controller ?
- A PID controller is an instrument used in industrial control applications to regulate temperature, flow, pressure, speed, and other process variables. PID (proportional integral derivative) controllers use a control loop feedback mechanism to control process variables and are the most accurate and stable controllers. PID control is a well-established way of driving a system towards a target position or level. It's practically ubiquitous as a means of controlling temperature and finds application in myriad chemical and scientific processes as well as automation. PID control uses closed-loop control feedback to keep the actual output from a process as close to the target or setpoint output as possible.