COURSE
Servo & Motion Control System
Sunset
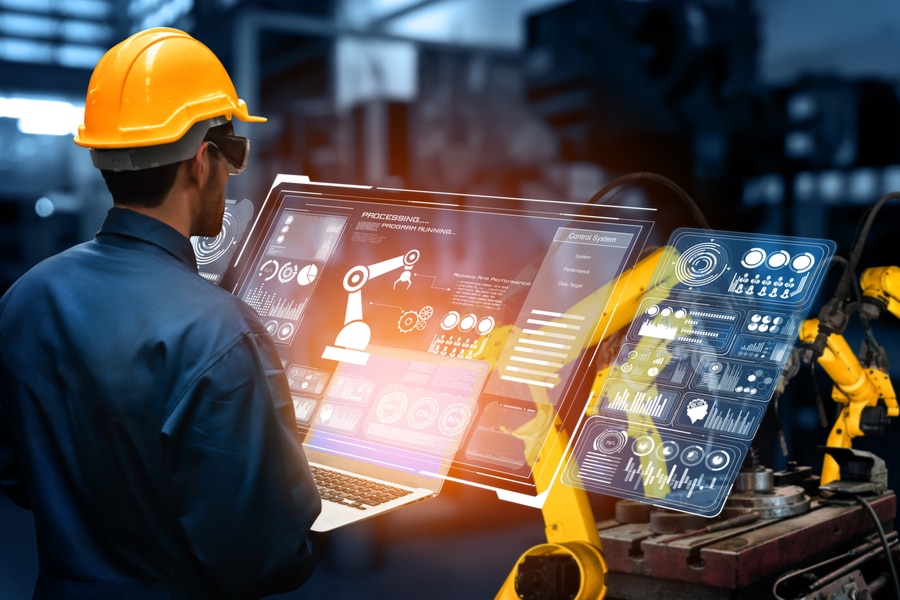
Beautiful
night

Sunshine
Vision Robotic India Pvt Ltd is one of the major training company in India that provides the best Industrial training and placement in the Advanced level Automation field. If you are planning to become an Advanced Automation Engineer then your better option would be to join our Advanced-level Industrial Automation Engineer course in Vision Robotic India Pvt Ltd.. If you complete the Advanced Industrial Automation Engineer course from Vision Robotic, you will get national & international certification. One of the major advantages of choosing a career in Automation is that it’s a good-paying job, better growth & sustainability in your career
Vision Robotic will provide a career path for freshers with a career path in the industrial automation Sector. This course will provide you with the required skills to perform in an industrial plant. During this course, you will get on-demand skills that will be useful for your future in industrial automation. You will be trained by industrial professionals and the syllabus of this course is designed by industrial professionals. You will be part of several industrial projects and this will improve your job-ready skills.
India is ready to turn into a worldwide assembling centre by offering boundaries like savvy assembling, quality, and severe conveyance plans. The least necessities to support in the worldwide market are a-list quality, severe adherence to conveyance plans, and minimal expense. To accomplish these three targets, there is no other option except to involve computerized machines for assembling.
As the Automation area increases steadily, every industry utilizes mechanized machines. There is no option for a robotized machine. Expanding demand for robotized machines results in expanding interest for machine producers. A client of a mechanized machine needs an upkeep designer to investigate the machines. A maker of robotized machines needs configuration engineers, developers, and administration engineers. Along these lines, in a perfect world, each assembling industry would like to utilize computerization engineers who investigate or configure control arrangements of machines without any help.
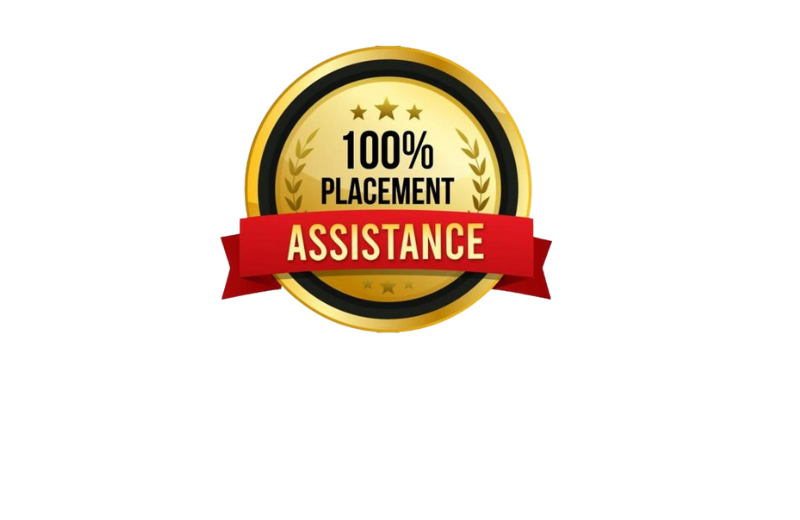
Course Contents
Servo Section:-
• Servo Drive and Motors: Selection, Architecture, converters & Inverters, Servo and Difference, etc.
• Technologies Content Electronic, Components: Diode, thyristor, transistor, IGBT DC, Encoders, etc.
• Keypad, Catalogue No. explanation, Commissioning of Servo, Reset to default Datasheet/Manual, Parameterization, etc
• Velocity Control Mode, Wiring and Programming, Running Servo in FWD/REV by 0 -10VDC etc.
• Position Control Mode via High-Speed IP, Circuit - Servo Position Mode, ON/OFF control using PLC, etc.
• Torque Control Mode in Servo Drive, Understanding Torque Control mode using 0 -10 VDC etc.
• Control Mode in Servo Drive, Digital Output Feedback Signal, Digital Output - Servo Ready Feedback etc.
• Digital Input - SERVO ON, Digital Input - Command Inverse, Running Servo in Reverse Direction, etc.
• Digital Output - Servo ON Feedback, Digital Output - Zero Speed Feedback, Digital Auxiliary Input Signal etc.
Motion Control Section:-
• Concepts of Machine Motion Control Systems in the Industries• Principle of the Basic Motion Systems used into the Industries
• Concepts of the different types of technologies using in the Motion Control System
• Introduction of the Different types of Motion Control Systems available in the Industries
• Introduction of the Applications of Motion Control Systems in the Industries
• Selection Criteria of the Motion Control Systems in the Industries
• Programming parameter, Hardware interfacing & Integration (HMI, PLC & Motion System) etc.
On-Site Practical Exposure
• Industry-1
• Industry-2
• Industry-3
Projects
• Level-1
• Level-2
• Level-3
** The above is the Lite syllabus and doesn’t cover the full syllabus. To get the full syllabus Book a Free Demo Now
Training on the followings Brands
Who Should Attend
- Programmers
- Erection & commissioning engineers
- Project Engineers
- Service Engineers
- Maintenance Engineers
- Machine Operators
- Software Engineers
- IoT developers
- Operation Engineers
- Application Engineers
Benefits of Training from us
- Designed for Working Professionals
- Personalized mentorship sessions
- Dedicated career support
- Doubt-Solving with Expert Industry mentors
- Proactive Program Support
- Job Assistance with Top Firms
- Syllabus is designed by Industry Experts
- Virtual Lab Facility
- 100% Placement Assistance
- National & International Certifications
Our Channel Partners
Frequently Asked Questions
What is Servo System?
- Servo motors or “servos”, as they are known, are electronic devices and rotary or linear actuators that rotate and push parts of a machine with precision. Servos are mainly used on angular or linear positions and for specific velocity, and acceleration.
Companies heavily use servo motors because of how compact and potent it is. Despite its size, it generates quite the amount of power and is known to be incredibly energy-efficient.
Most of the companies that use servos are manufacturing companies that need them to position control surfaces and rotate objects at precise angles and distances. Most of the companies that use servo motors are manufacturing companies that use machines with servo motors.
What is Motion Control System?
Motion control is the process of moving machinery using rotary and linear actuators. Motion Control is a sub-field of automation whereby position or velocity machines are controlled using a motion control device, such as a linear actuator, electric motor, hydraulic pump, or servo motor. Motion control encompasses every technology related to the movement of objects.
Motion control is also referred to as Servo Control or Robotics and is implemented in industrial processes to move specific loads in a controlled way. A motion control system comprises a control, a drive, a motor, and a load.
What is IGBT?
- An insulated-gate bipolar transistor (IGBT) is a three-terminal power semiconductor device primarily forming an electronic switch. It was developed to combine high efficiency with fast switching. It consists of four alternating layers (P–N–P–N) that are controlled by a metal–oxide–semiconductor (MOS) gate structure.
What is Position Control Mode in Servo?
The position loop regulates the position of the motor or system. In Position mode control, feedback such as an encoder or resolver ensures that the actual position is equal to the commanded position. The servo drive’s position loop compensates for position errors by applying more torque to push the system back into position. If an outside force acts on the motor shaft, the drive will “fight back” to maintain the target position.